Affiliate Disclosure: Automoblog and its partners may earn a commission when you use the services or tools provided on site. These commissions come to us at no additional cost to you. See our Privacy Policy to learn more.
As the first quarter of 2023 draws to a close, the auto chip shortage continues to be one of the biggest storylines in the automotive industry. In early March, automotive trend analyst group AutoForecast Solutions announced that the projected number of vehicles cut from North American production cycles had nearly tripled as a result of the shortage.
Sam Fiorani, Vice President of Global Vehicle Forecasting for AutoForecast Solutions, is one of the world’s leading experts on the automotive supply chain. Automoblog sat down with Fiorani to get his perspective on where things are with the semiconductor supply, its impact on the auto industry, the factors that contribute to it, and when the chip shortage could finally end.
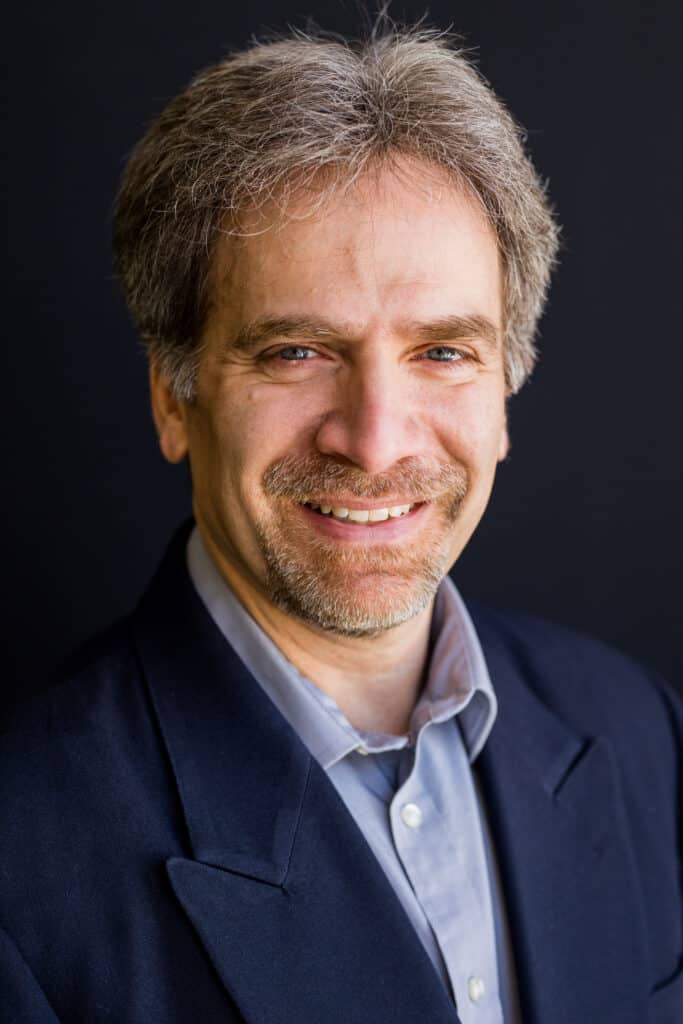
As we move into Q2 of 2023, how would you describe the status of the automotive chip shortage?
“Moving into the third year of the chip shortage, things are improving. The industry has seen continual improvements – from nearly 10.6 million units pulled from production plans in 2021 to an expected 2.8 million lost this year.
With better supplies of chips for car and truck use, the global losses in 2024 could be as little as one million, or just over 1% of the expected production. Diligence on the part of automakers and suppliers will keep the industry moving ahead.”
What are some of the most noticeable ways that the shortage is impacting the auto industry?
“The lack of chips has been a significant limiting factor on the dramatic inventory shortage over the last three years in North America. Available chips have been fed into higher profit models, leaving more affordable vehicles in short supply.
Many of the vehicles that have actually made it to dealers have been lacking components such as cylinder deactivation systems, heated seats, heated steering wheels, and even navigation systems in some instances.”
Which factors currently have the biggest impact on the semiconductor supply chain?
“When the pandemic shut down the economy, vehicle manufacturers were so sure that the market for cars and trucks wouldn’t bounce back quickly that they canceled orders for parts like semiconductors. This industry is not used to not being the focus of its suppliers, but chip producers don’t see automotive production as a priority. Automotive-grade chips are, typically, older designs for reliability.”
These older designs are less profitable than the chips used in smartphones and gaming systems. When vehicle manufacturers tried to turn on the supply chain, there weren’t enough chips because the fabs [factories that produce semiconductors] that make them focused on the newer chips. New fabs cost tens of billions of dollars and take years to establish, further delaying the supply of chips for vehicle use.
Where have you seen improvements over the last three years in vehicle supply chains?
“A number of vehicle manufacturers have established deals with chip makers to ensure the supply of semiconductors, while others just expected the situation to rectify itself. The U.S. government, through the CHIPS Act, is pushing for more investment in semiconductor development and production locally instead of relying on chips imported from China and Taiwan. While these will take time, they are steps in the right direction.
What needs to happen for the chip supply chain to reach a point of stasis or even surplus?
Establishing new fabs to make chips takes time and lots of money. The investment is heading in the right direction, so now we’re just waiting for the capacity to be built. Some newer vehicles have moved toward more modern chips, which also helps increase the supply since those are the chips the industry would like to make.
A post-shutdown lag in demand for computers and gaming consoles has opened up some supply of these chips, but it’s the older chips that are in the highest demand for automotive use, and that supply is still lagging behind the demand.”
Should chipmakers be concerned about a rebound surplus in the future?
“With the proliferation of web-enabled and computer-controlled devices, the long-term growth in demand for semiconductors is fairly well established. There’s always a risk of oversupply, but this is unlikely for the rest of this decade, as chip demand for automotive use is expected to nearly double the industry’s share of the chip market.”
What impact would a fully-recovered chip supply have on individual consumers?
“Buyers are getting acclimated to ordering vehicles or paying well over sticker [price] due to the lack of inventory. When the chip supply recovers, competition between manufacturers and between dealers will likely return inventory levels to something more closely resembling 2019.
The industry promises that they’ve learned from past mistakes, and we won’t see 60-day supply of cars and 100-day supply of trucks on dealership lots, but the current level of 30-day supply is unsustainable. Expect dealers to carry between 45- and 60-days’ supply of vehicles when production returns to normal levels.”
What are automakers and dealers doing, if anything, to prepare for future shortages like this? What should they be doing?
“As one of the most important in the global economy, the automotive industry can be rather arrogant. Semiconductors are anomalies, as most components are supplied to vehicle manufacturers by companies that focus on the automotive industry. There aren’t many components like chips, where vehicle production has to compete with non-automotive industries.
Securing more fabs dedicated to vehicle chips will go a long way to stabilizing the supply of semiconductors. But the ties to the chip industry need to be maintained in order to maintain the cutting-edge technology developed for other industries.”
In your opinion, when do you expect the chip supply to fully recover?
“Issues from semiconductors should be minor in 2024, but there will still be some residual problems, such as missing components and systems. If all goes according to plan and additional capacity is established, vehicle production should have adequate access to chips by 2025.”